六角フランジボルトとは?六角フランジボルトの特徴や加工方法をご紹介!
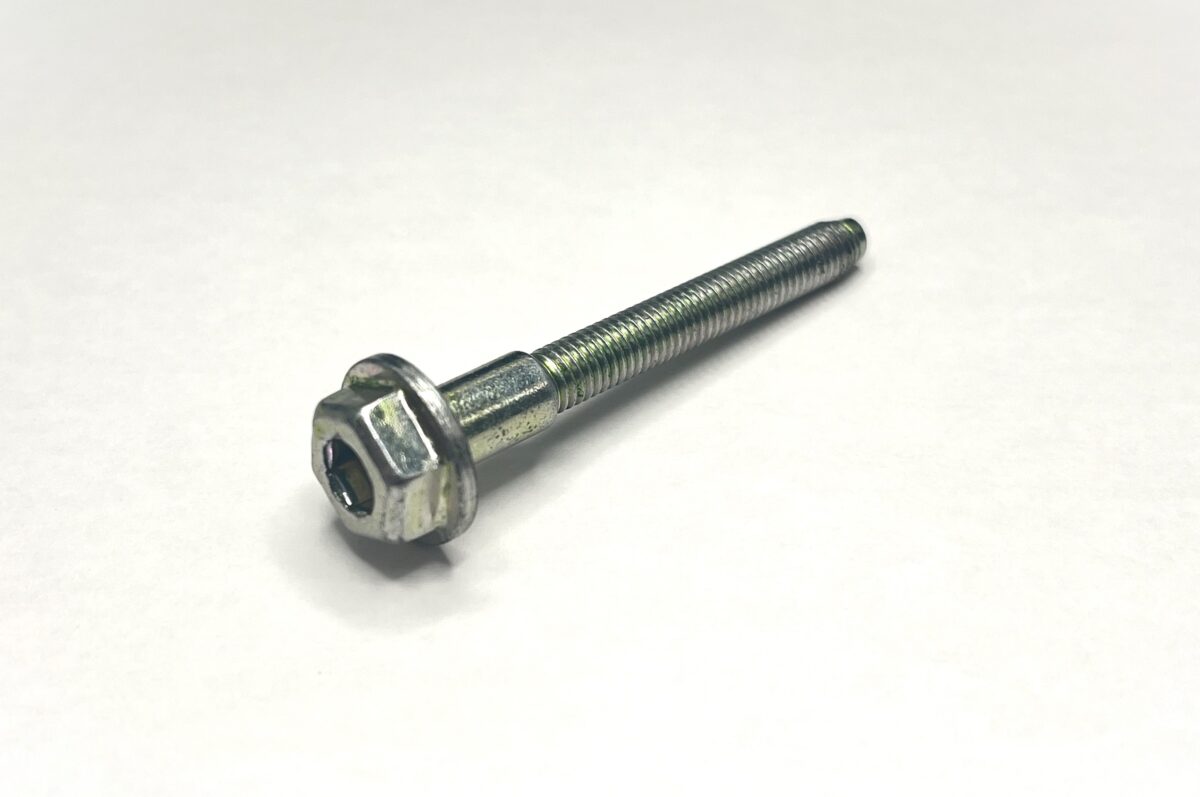
六角フランジボルトとは、その名の通り頭部形状が六角のフランジ付きのボルトのことを指します。
フランジ付きのため、座金(ワッシャー)がなくと緩み止め効果が高いことが特徴です。
ここでは、六角フランジボルトの特徴や、六角フランジボルトの製作方法、そして実際に当社で製作した六角フランジボルトの製品事例まで、まとめてご紹介いたします。
六角フランジボルトとは?六角フランジボルトの特徴をご紹介!
六角フランジボルトとは、その名の通り頭部形状が六角のフランジ付きのボルトです。
また、フランジボルトとは、フランジと呼ばれる”つば”がネジ頭部の下についているボルトです。このフランジにより、相手材との接触面積を増やすことができ、摩擦力を高め緩み防止を実現することができます。
また、フランジボルトは座金(ワッシャー)を取り付ける必要がなく、フランジがボルト本体と一体化となっているため、座金を取り付ける手間を省くことができます。
通常、フランジボルトは六角形の頭部や六角穴となっていることが多いですが、フランジボルトでも頭部が六角以外のものもございますので、頭部が六角のものは「六角フランジボルト」あるいは「フランジ付き六角ボルト」と呼ばれています。
六角フランジボルトは、緩み防止に効果があるため、振動のある箇所や耐久性が求められる厳しい環境下でも安定した性能を発揮します。
六角フランジボルトの加工方法をご紹介!
六角フランジボルトは、頭部、フランジ部分、ネジ部の大きく3つに分かれますが、基本的なボルトと同様で、切削もしくは圧造で製作されます。
頭部の六角部分、フランジ部分は特にヘッダー加工を用いて製作します。ネジ部は転造で加工することができます。
六角穴の部分は、円形状に凹んでいます。内側をへこませることで外側のエッジを立たせることができ、六角部の精度を高めることができます。
圧造、ヘッダー加工や転造での加工について、特殊ネジ カスタム部品製造.comでは多くのノウハウがございます。詳しくは下記記事をご覧ください。
>>フォームローリング加工とは?転造との違いから特徴まで解説!
特殊ネジ カスタム部品製造.comだからこそできる六角フランジボルト
当サイトを運営する太陽精工株式会社では、これまでに数多くの特注の六角穴フランジボルトの製作を行ってまいりました。当社だからこそ可能なフランジボルトの特徴をご紹介いたします。
様々な頭部形状への対応
六角穴以外にも、様々な頭部形状の製作が可能です。ヘッダー加工により頭部を成形しますので、様々な頭部のフランジボルトの製作を行うことができます。
- 頭部がナベ頭
- 頭部がトラス
- 頭部に十字穴付き
- 頭部にヘクサロビュラ(トルクス)付き
- 頭部が低頭
当社のヘッダー加工技術は、国内外のメーカーからも評価が高く、お客様から選ばれる理由の1つでもあります。
メーカー規格外の特注フランジボルト
フランジボルトを製作する場合、規格品であれば圧造での製作が可能ですが、ボルトの径やネジ部分が一部特殊だったり、軸部分の径や長さが特殊になると、すぐに規格品から外れてしまい、通常の圧造加工では加工が難しく切削で加工を行うことになり、思ったよりコストがかかってしまったという事態が発生します。このような軸部分とネジ部分における径や長さが規格外の場合は、ネジメーカーに製造依頼をする必要があります。
当社では、独自の2ダイ3ブロー技術をベースとしたヘッダー加工や、転造加工、フォームローリング、様々な追加工により、メーカー規格外の特注のフランジボルトの製作を行っております。下記はその参考例です。
- 胴部が長く、ネジ部が短い
- ネジ部が短寸
- 不完全ネジ部が非常に短い(1ピッチ以下)
- 横穴付き
また特注のフランジボルトの場合、切削加工による追加工でどうしてもコストが高くなってしまっている場合も多いのが現状です。しかし当社では、切削加工から圧造加工への工法転換により、大幅にコスト削減をした事例も多数ございます。
多種多様な材質・メッキ・表面処理の六角フランジボルト
段付きの形状自体は通常の規格品で材質が規格外という段付きボルトについても、当社で多くご相談をいただいております。材質については、合金鋼、ステンレス、アルミ、チタン、銅など、様々な材質の冷間圧造加工に対応しております。
またメッキや表面処理についても、当社独自のネットワークを駆使して、お客様のご要望に最も最適なメッキ・表面処理方法をご提案いたします。
不完全ネジ部が最小化されたフランジボルト
フランジのあるネジ部が短いボルトは、全体のバランスが悪く、転造加工でネジ山を加工すること自体の難易度が上がります。その上で不完全ネジ部を極力抑えなければいけない場合、転造加工に相応の工夫をしなければいけません。
当社では、このようなバランスが悪いフランジボルトであっても、不完全ネジ部を最小化する独自の転造加工によって、段形状のショルダー部のギリギリまでネジ山を立てることができます。不完全ネジ部を最小化した高精度段付きボルトへの対応力は、当社が国内大手メーカー様からも直接ご注文をいただくことができる理由の1つだと考えております。
軽量化されたフランジボルト
カーボンニュートラル実現に向け、エネルギー高効率化の観点より様々な部品での軽量化が求められています。ボルト等の締結部品もその例外ではありません。例えば30,000個の部品を要する自動車部品の中で、約2,000~3,000個が締結部品にあります。1本あたりの重量0.5gを軽量化させると、おおよそ車体重量1kgの軽量化につながることになります。このように材質による軽量化だけでなく形状による軽量化を考えていくことが、今後の課題になります。
フランジボルトにおいては、アルミに材料変更したり、袋穴で一部中空にするなどの工夫を施すことで、段付きボルトの軽量化を実現することができます。
六角フランジボルトの事例のご紹介!
続いて、実際に当社で製作した六角フランジボルトの事例をご紹介いたします。
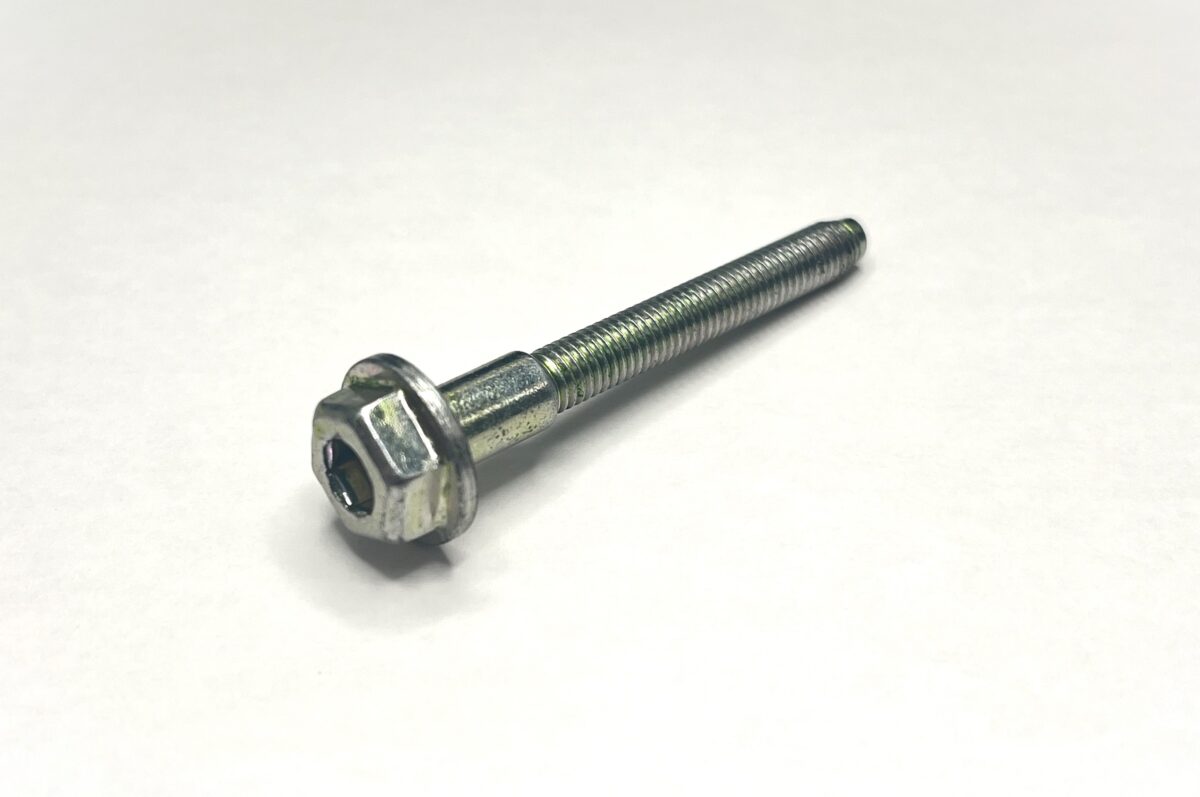
六角穴付六角フランジボルト
こちらの製品は、六角穴付六角フランジボルトです。
本品の用途はミリ波レーダーの調整用ボルトです。相手材との座面密着面積を稼ぐために頭部がフランジ仕様になっています。首下段部は貫通した部品が通るスペーサーの役目をしています。
調整用ボルトということでM5ネジ部はトルク安定剤のトルカーが塗布されており・・・
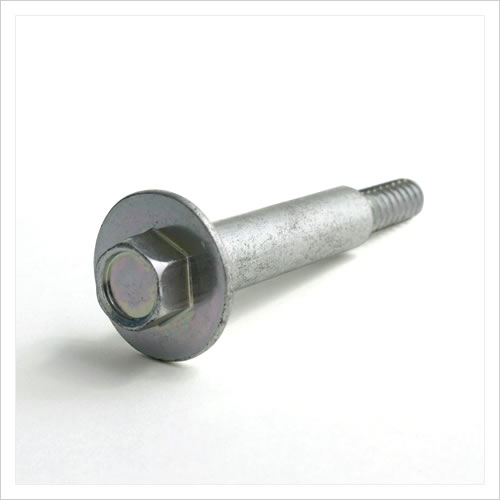
六角フランジ長寸段付きボルト
こちらの製品は、六角フランジ長寸段付きボルトです。
本製品は洗濯乾燥機の支柱になるボルトです。六角の対辺がM6相当(10−0.2)の寸法に対し、フランジ部がM16相当(24.49−0.35)のギャップで製造されております。
ポイントはフランジ部の座面径ですが、ねじの軸部が長いことで、冷間圧造機械の中での搬送が難しいため・・・
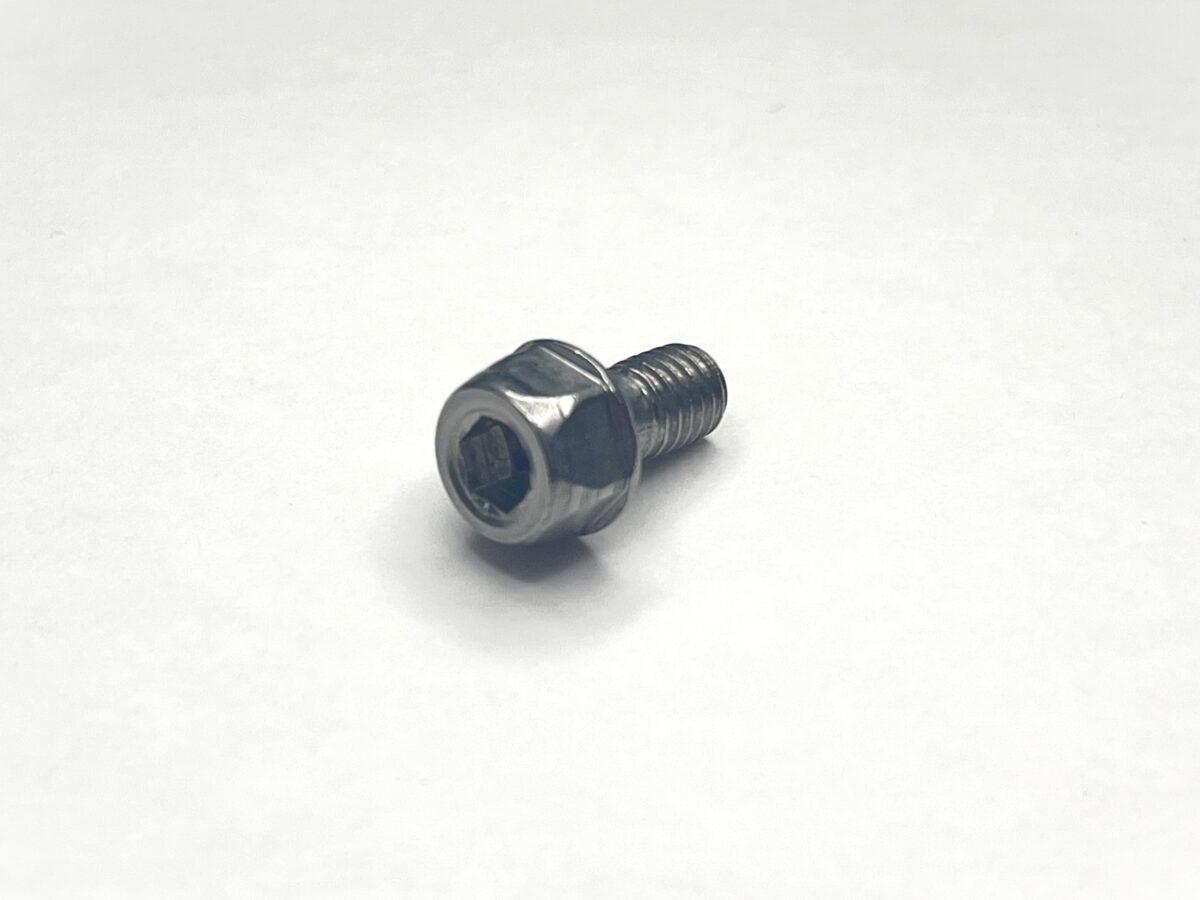
六角穴付六角小フランジボルト
こちらの製品は、六角穴付六角小フランジボルトです。
この商品は工具穴形状が六角穴、頭部形状も六角頭で、またフランジも付いた特徴的な形状をしたボルトです。本形状の理由としてはモビリティの前変速機の狭小箇所で使用されるため締め付けが非常に困難であるため、六角穴で六角レンチでも締め付けられる、また頭部六角形状でスパナでも締め付けられる便利な仕様にするためです。
六角フランジボルトのことなら、特殊ネジ カスタム部品製造.comまで!
六角フランジボルトでお困りの際は特殊ネジ カスタム部品製造.comを運営しております太陽精工株式会社までお気軽にお問い合わせください。
◆特殊ネジ カスタム部品製造.comは、冷間圧造技術のノウハウと、オリジナリティ溢れる金型設計力、幅広い調達ネットワーク、そして積極的なVA/VEによる技術提案を行い、多種多様な特殊締結部品の製造を、試作開発から量産までトータルサポートさせていただきます!
>>当サイトについて
◆私たちの強みが形となった「冷間圧造」「2ダイ3ブロー」「ヘッダー加工」「転造加工」…など当社のサービス一覧をご紹介します!
◆私たちは冷間圧造を中心として特殊ネジ カスタム部品の製造を得意としております。特に、「目利き力」でお客様の求める製品の最適な製造方法をご提案させていただきます。実際、工法転換や材質変更などによる大幅なコストダウンを実現した事例が多数ございます!
◆特殊ネジ カスタム部品の設計・製造に関して、実際にお客様からいただいたご質問と、その回答を掲載しております!
◆当社の対応しております製品一覧をカタログにしておりますので、更にご興味ある方は是非ご覧ください。無料でダウンロードできます!
◆特殊ネジ カスタム部品の製造や工法転換など、お困りの際はお気軽にご相談ください!