転造で行う溝加工は”過酷で理不尽”!?その理由を技術的な視点で解説!
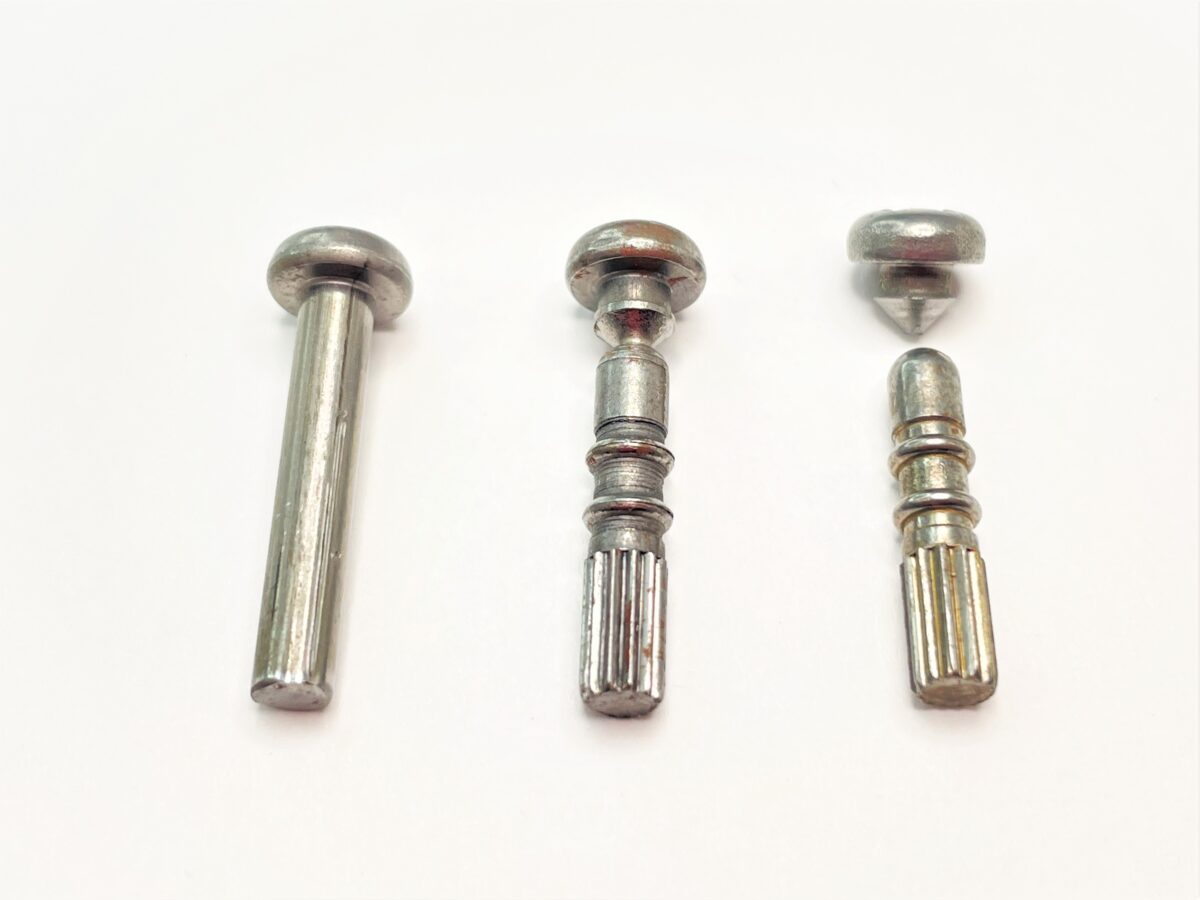
転造で行う溝加工はある意味では「過酷で理不尽」です。
なぜ過酷で理不尽なのか、その溝加工ならではの難しさの理由を本記事では解説しております。
この記事を読み終える頃には、転造加工が如何に簡単ではないのかがお分かりいただけるかと思います。
技術的な視点で、詳しく解説しておりますので、是非、最後までお読みください!
転造加工とは?
まずは転造加工について解説します。
転造加工とは塑性加工の一つで、素材に強い力を加えて盛り上げて成形する加工方法です。材料の可塑性を利用して、転造ダイスを回転している加工対象物に押し当てる技術です。転造加工は切削加工と比較すると、生産性が高く、加工品質が安定しているため、ネジや歯車等の回転対象体の部品加工に広く用いられています。
特に、ネジ(マシンスクリュー)転造加工は、山と谷の体積がほぼ同じ(正しくはごくわずかに違う)ことが特徴で、平ダイスの凸形状の山(※画像左)がが平坦なワークを押し込み肉をすぐ横に盛り上げることができるため、これらの繰り返しで、谷と山が成形されていきます。
更に詳しく解説しますと、この変形は平ダイスの「食い付き部テーパー」によって、転がりながら徐々に行われるため、谷部分が浅いところから深くなるにつれて、押しのけられた肉がすぐ隣に盛り上がります。詳しい解説については下記記事で行っておりますので、是非合わせてご覧ください。
溝加工を行うためのフォームローリング加工
転造において、溝加工を行う際に用いられ方法、加工がフォームローリング加工です。
フォームローリングはこの転造加工をさらに進化させた加工方法となります。
従来であれば切削加工で仕上げた溝形状も、フォームローリングであれば様々な溝形状が対応可能となります。また1回のフォームローリング加工で、異なるネジサイズの同時加工、複数の溝加工、溝加工と軸の先端加工、溝加工と切り飛ばし加工等の複合加工も可能となるケースが数多くあります。
このように複雑な形状をフォームローリングで実現可能とするためには1回の転造加工での製品の転がり回数が重要なポイントとなります。形状にもよりますが一般的なネジ山加工の2~3倍の転がり数が必要です。フォーローリング加工については、下記記事でも詳しく解説しておりますので、是非合わせてご覧ください。
>>フォームローリング加工とは?転造との違いから特徴まで解説!
フォームローリング加工はある意味で「過酷で理不尽な転造加工」と言えます。最もシンプルな形状なのに最も過酷で理不尽な加工の代表が、溝入れ転造加工です。
なぜ過酷で理不尽なのか、次の段落で解説します。
溝部の肉は何処に行く?
溝加工の際に、生じた肉の逃げ場はどこでしょうか?加工反力に対して機械剛性が低ければ、わずかに盛り上がることもできますが、製品的には盛り上がらないようにしたい場合の方が多いかと思います。
例えるなら、穴を掘って出た土砂を、近くに山積みにしてはいけない状況にも似ていますが、この余った肉はどこに消えるのでしょうか?
結論としては、製品は伸びるしかありません。特に、表面に近いところが伸びいやすく、対照的に中心部は伸びにくく、特に太くなればなるほど伸びにくいです。
中心に近いほど加圧点から遠くなり、また、反対側からの反力をより多く受けるために、表面近くは伸びやすくなります。また、溝入れピンの先端部にくぼみが生じるのも、この原理が働くためです。
溝の位置は、この伸びやすさ、伸びにくさに大きく影響を与えます。
軸の先端や首下に近い溝は伸びる逃げ場が近いのに対して、先端や首下から離れた溝の場合は端に行きつくまでに、あまりにも多くの表層肉を押し出さなければならず、大きな抵抗がかかります。
なお、先端部にフラット部(先平)が必要な場合は、切り刃を持った「溝入れ&切り飛ばしダイス」としてダイスを設計しますが、この時、十分に伸ばした後で切り飛ばさないと、切り刃が欠けやすくなります。
そのため、溝だけのダイスよりも、2~3転がり余計に転がり長さを設ける必要性があります。1クラス上の平ダイスとマシンが必要になるのはこのような理由があります。
逆に、無理に短いダイスで設計すると切り刃の寿命が短くなってしまいます。
材質が硬かったり【45KやXM-7】、加工硬化の激しい材質の場合は、さらにこの問題は顕著になります。
また、肉を押しのける難しさは、素材の硬さのほかにも、溝の幅と溝の深さが大きく影響します。
溝幅が広ければ広いほど、また、溝が深ければ深いほど、肉は動きにくく、加工抵抗は増えます。ですから、「長い軸の中央部に幅広の溝を入れる」という加工は、最も過酷なのです。
フォームローリング加工が難しい理由
たとえいかなる局面においても、それが、転がり摩擦抵抗の限界を超えてはいけません。超えた瞬間に、ワークは転がらずに滑ってしまい、その瞬間に、良品とならない事が確定します。
そのため、ボンデなどのワイヤー材の潤滑被膜の(※下図)、転造加工は、非常に難易度が高いです。圧造加工に必要なこれら皮膜を転造加工前に取り除くことが、限界領域の過酷な転造加工では、成功させるためには有効な対策になります。
このように転造の真実がわかってくると、転がして加工できるのは当たり前ではないとわかるかと思います。
当社ならではのフォームローリング加工とは?
特殊ネジ カスタム部品製造.comを運営する太陽精工では、当社ならではのフォームローリング加工を展開しております。
様々な形状への加工に対応可能
転造加工ではネジ山への加工のみになりますが、当社のフォームローリング加工では、下記の様な形状に対応可能です。
- 溝入れ
- 棒先
- 尖り先
- 丸先
- 球成形
- 寸切り
- セレーション
- ローレット
このようにフォームローリング加工では、従来は切削加工のような二次加工でしかできないと考えられていた形状も加工することが可能です。
同時に加工する複合フォームローリング加工
また工夫を凝らすことで、1回のフォームローリング加工で異なるネジサイズの同時加工も可能となります。また複数の溝加工や、溝加工と軸の先端の同時加工、さらには溝加工と切り飛ばし加工といった加工も同時に実現することができます。このような複合フォームローリング加工の技術提案力も、当社ならではの特徴だと考えております。
長いストロークを有するフォームローリング加工機を多数保有
先述のように、複雑な形状をフォームローリングで実現可能とするためには1回の転造加工での製品の転がり回数が重要なポイントとなります。形状にもよりますが一般的なネジ山加工の2~3倍の転がり数が必要です。
太陽精工では、ストロークを有するフォームローリング機を多数持ち合わせておりますので、幅広いフォームローリング加工に対応可能です。
フォームローリング加工への工法転換によるコストダウン
上記のように、形状や加工方法への提案力と設備力を掛け合わせることで、太陽精工だからこそ可能なフォームローリング加工技術を構築してまいりました。この独自のフォームローリング加工技術によって、切削加工からフォームローリング加工への工法転換も可能となり、その結果として多くのコストダウン実績を積み重ねてきました。
溝加工・フォームローリング加工を用いた事例のご紹介!
続いて、実際に当社で溝加工・フォームローリング加工を用いた技術提案事例と加工事例のご紹介をいたします。
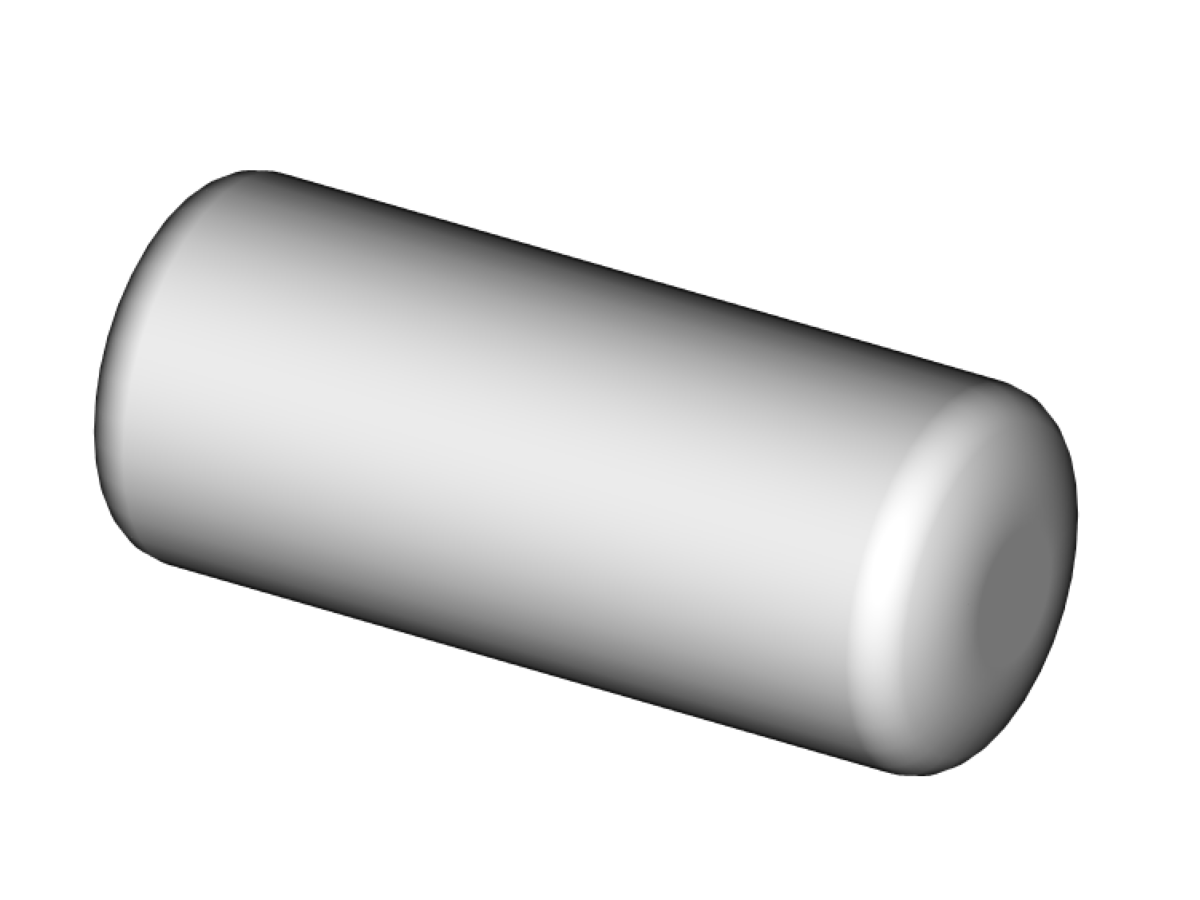
技術提案事例:切削品を3カ所同時フォームローリングへの工法転換で50%コストダウン
こちらはバー材からの全切削で製造コストが非常に高かった製品に対して、切削加工からフォームローリングへの工法転換することで50%コストダウンを実現した技術提案事例です。
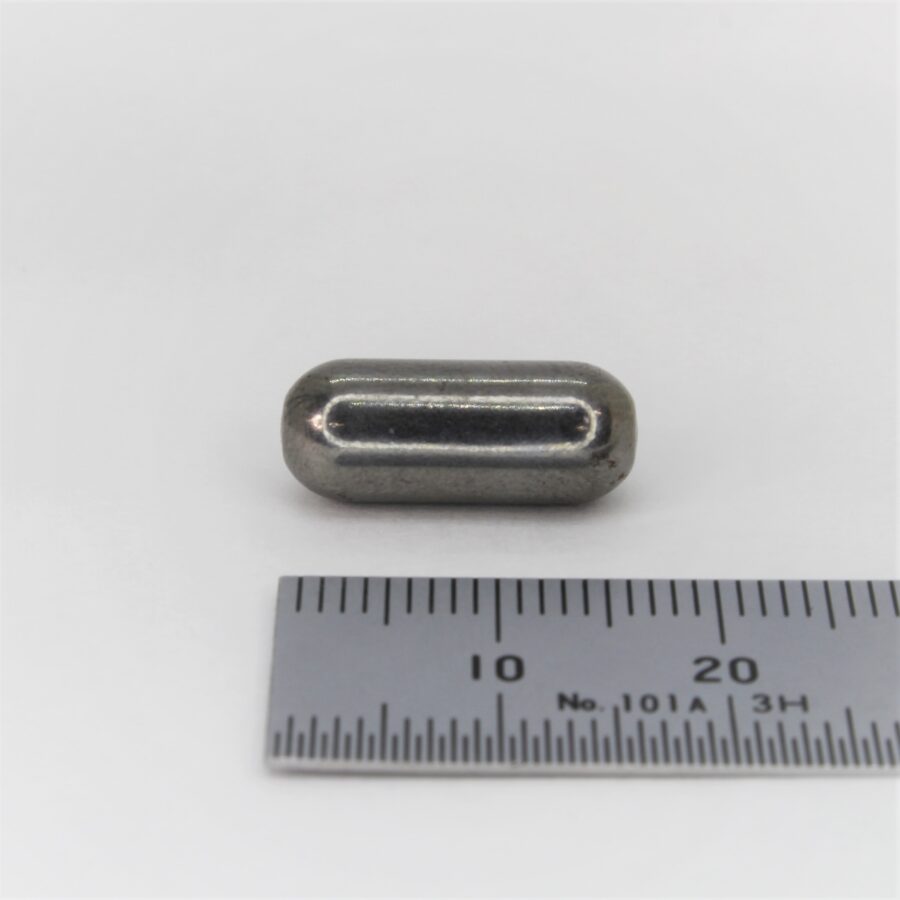
加工事例:フォームローリングピン(φ7)
こちらは自動車向けのフォームローリングピンです。写真の通り、両端にR3.5が必要な製品です。
お客様からご相談いただいた際は、元々はバー材からの切削をしていた製品とのことでしたが、コストダウンを希望されて当社にご相談いただきました。そこで当社からは、まずリベットを圧造し、その後当社固有のフォームローリング技術により、1工程(1パス)で両端にR付け加工をして生産いたしました。その結果…
転造加工のことなら、特殊ネジ カスタム部品製造.comまで!
転造加工でお困りの際は特殊ネジ カスタム部品製造.comを運営しております太陽精工株式会社までお気軽にお問い合わせください。
◆特殊ネジ カスタム部品製造.comは、冷間圧造技術のノウハウと、オリジナリティ溢れる金型設計力、幅広い調達ネットワーク、そして積極的なVA/VEによる技術提案を行い、多種多様な特殊締結部品の製造を、試作開発から量産までトータルサポートさせていただきます!
>>当サイトについて
◆私たちの強みが形となった「冷間圧造」「2ダイ3ブロー」「ヘッダー加工」「転造加工」…など当社のサービス一覧をご紹介します!
◆私たちは冷間圧造を中心として特殊ネジ カスタム部品の製造を得意としております。特に、「目利き力」でお客様の求める製品の最適な製造方法をご提案させていただきます。実際、工法転換や材質変更などによる大幅なコストダウンを実現した事例が多数ございます!
◆特殊ネジ カスタム部品の設計・製造に関して、実際にお客様からいただいたご質問と、その回答を掲載しております!
◆当社の対応しております製品一覧をカタログにしておりますので、更にご興味ある方は是非ご覧ください。無料でダウンロードできます!
◆特殊ネジ カスタム部品の製造や工法転換など、お困りの際はお気軽にご相談ください!