切削品を3カ所同時フォームローリングへの工法転換で50%コストダウン
こちらはバー材からの全切削で製造コストが非常に高かった製品に対して、切削加工からフォームローリングへの工法転換することで50%コストダウンを実現した技術提案事例です。
バー材からの全切削で製造コストが非常に高い...
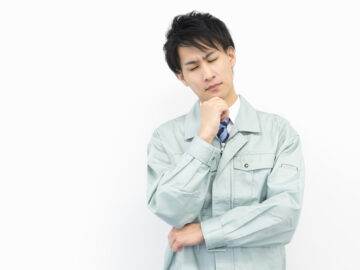
今回の製品は、一般的な冷間圧造では製造が困難な製品のため、バー材からの切削により製造されていました。しかし全切削では製造コストが非常に高くなってしまいます。
そのためこちらの特殊締結部品のコストダウンをしたいということで、当社にご相談いただきました。
フォームローリングへの工法転換で50%コストダウン!
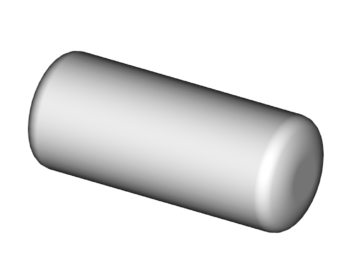
そこで太陽精工からは、切削加工からフォームローリングへの工法転換をご提案いたしました。具体的には、まず圧造でブランクを製作し、次に転造加工でもみ切りながら頭部のR加工を行う工法です。当社では圧造加工のみならず、このように転造加工においても技術提案を行っております。
この工法転換によって、50%のコストダウンに成功しました。また納期面も不安定だったところが安定するようになり、お客様から安心いただいてリピートにもつなげることができました。
一般的な冷間圧造・転造加工では困難な形状であっても、当社では切削レスで想いを形にいたします。今回の製品においても、長年模索・探求し続けてきた転造技術により、1工程で3カ所の転造加工を行っております。
このような既存品のコストダウンにもお応えいたしますが、当社では新規開発製品の量産前試作で一番力を発揮すると考えております。量産前段階であれば、金型設計からのご提案を行うことができるため、より大きなコストメリットを生むことができると確信しております。
特殊締結部品の試作開発・量産前試作でお困りの方は、ぜひお気軽にお問い合わせください。