アルミツバ付きスペーサーを全切削⇒2ダイ3ブローに工法転換し、50%コストダウン!
こちらは、 従来はバー材からの切削加工を行っていた、頭部径と軸径のギャップが大きいアルミ製ツバ付きスペーサーに対して、 全切削 ⇒ 2ダイ3ブローに工法転換することでコストダウンし、切削レスで50%コストダウンに成功した技術提案事例になります。
頭部径と軸径のギャップが大きく、全切削で加工しているものの、コストが高い...
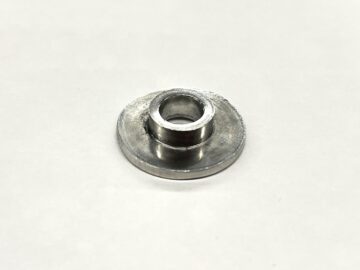
お客様より、アルミ製スペーサーのコストダウンについてご相談をいただきました。従来はバー材からの切削加工を行っていたとのことでしたが、頭部径と軸径のギャップが大きいことから、削り代が大きく、単価がなかなか下がらないとのことでした。そこで、切削品を圧造で製造することは可能か?とのお問い合わせをいただき、案件化しました。
全切削 ⇒ 2ダイ3ブローに工法転換することでコストダウン
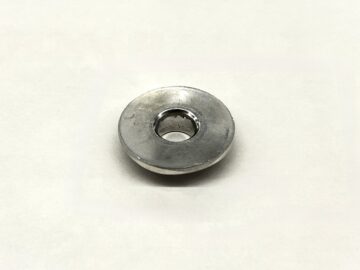
そこで当社からは、アルミ製スペーサーを全切削 ⇒ 2ダイ3ブローに工法転換するご提案をいたしました。切削品から圧造への工法転換だったため、角や細かいRに対して、弊社から細かく仕様を確認の上でご提案いたしました。
今回の材質はA5052(アルミ)だったため、圧造機内で貫通穴を開けることができました。これにより切削レスになり、単価をぐっと抑えることが出来ました。また内径貫通の際に、天面側の内径にパンチでC面をつけることで、天面側に生じる内径のバリを抑えました。
今回の製品は当社としては径が大きいものになりますが、無事に2ダイ3ブローにて対応することができました。ツバ付きで頭部径が比較的大きいスペーサーだったため、当初は径を満足することができるかという点が課題でしたが、細かな予備成型の調整やパンチ側への工夫を施すことで、実現させることができました。
また懸念点だった貫通穴を抜いた後のバリについても、C面取りをすることでバリを抑えられるよう対応できたのも、お客様から評価いただいたポイントです。