溶接ナットからカシメナットに変更して品質向上&コストダウン!
こちらは、溶接ナットをカシメナットに変更することで、品質向上とコストダウンを両立した事例となります。
溶接ナット使用時の課題とリスク
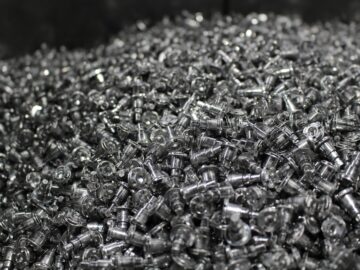
自動車業界では、車両の軽量化のため、普通鋼板から高張力鋼板への設計変更が増加しています。以前は溶接ナットが広く使われていましたが、以下のような課題に直面していました。
- 高張力鋼板への溶接は割れやすく、安定した溶着が困難でした。 これにより、溶接不良が発生し、品質基準を満たせないケースがありました。
- また、同様に増えてきたメッキ鋼板を使用する場合、メッキ同士の溶接は非常に不安定で、組合せ後にナットが外れる「剥離不具合」が発生していました。
- 溶接時に発生するスパッタがネジ部に付着し、ネジが通らないといった品質懸念や、溶接熱による母材の変形・変質も問題でした。
- 一部の溶接ボルトでは、溶接時に頭部が飛んでしまう危険性もあり、作業の安全性も課題となっていました。
これらの問題により、特定の材料や条件下では溶接ナットの使用が難しく、生産ラインでの品質安定化が大きな課題となっていました。また溶接工程はCO2が発生してしまうため、環境問題への懸念から自動車メーカーが溶接ナットの代替策を検討されていました。
カシメナット導入によって品質向上&コストダウン、さらに脱炭素にも貢献!
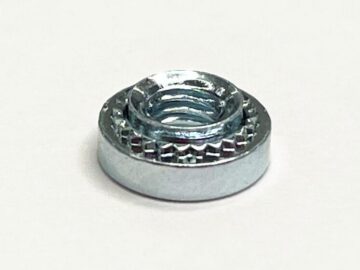
溶接ナットからカシメナットへ変更することで、お客様は以下のような具体的なメリットを享受できるようになりました。
メリット①:スパッタ対策が不要になくなる
溶接に伴うスパッタがなくなるため、清掃作業等にかかる時間とコストを削減できました。
メリット②:製品への熱影響がない
熱による母材の変形や脆弱化の心配がなくなり、特に高張力鋼板の特性を損なうことなく締結が可能になりました。
メリット③:CO2排出量削減に貢献
溶接工程が不要になることで、CO2排出量の削減にも貢献できました。
さらに、溶接ナットからカシメナットに変更することで、以下のような効果も実現しています。
- 溶接後の剥離やネジ不通といった不具合が解消され、品質の安定化に大きく貢献しました。
- カシメナットは順送プレスの工程内で加工できるため、工程の短縮化と生産能力の安定化を図ることができました。
カシメナットは、薄板やタップ加工が困難な母材への締結に適しており、特に高張力鋼板やメッキ鋼板を使用する際に課題だった溶接課題を解決することができます。また溶接ナットが抱える熱影響やスパッタ、歪みといった問題点を回避できるだけでなく、品質の安定化、生産工程の短縮、そしてCO2排出量削減といった多岐にわたるメリットをもたらします。
お客様の中には、既存の規格品にはない厚みや径、段付き・中溝といった、特殊形状のカシメナットが必要なケースもございます。当社ではお客様の仕様に合わせた製造体制により、設計通りの最適なカシメナットを製造しております。また、お客様の使用環境によっては溶接ナットとカシメナットの使い分けが重要になりますが、当社はでお客様の多様なニーズに応え、規格外の特殊なカシメナットも柔軟に製造対応しております。
カシメナットに関するより詳しい情報は、製品事例ページやコラムページをご覧ください。